About US
Home / About Us
Our team concentrates on polymer extrusion equipment and process technology; together with our professional technicians and staff, we are dedicated and passionate about our mission. Since the creation of the company, we have worked with energy and devotion towards developing innovative, sustainable, and environmental-friendly solutions, aspiring to become pioneers in the industry.
Our customers, including several Fortune 500 companies, have reported satisfied reviews of our service and expertise with providing advanced polymer extrusion technology and extensive solutions. Our performance is never occasional, but consistent, allowing us to become one of the most advanced extrusion technology companies in China and a global leader in the industry.
Our team’s diverse backgrounds and vast experiences eliminate potential mistakes and guarantee our clients with the most efficient, effective, effortless production solutions.
The USEON team welcomes you with our multilingual technical service team and more via email, telephone, or video conference.

Mission
Be the first choice for the customers of all our business units;
Create value by GREEN TECHNOLOGY;
Make a positive difference to“made-in-China”.
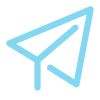
Value
Responsibility, Team, Innovation
Responsibility
Responsibility for our customers and for Useon is our most important value that guides our work. We are responsible for our customers’ success. We are responsible for Useon’s healthy growth. Being responsible is our dynamic to do our work better. We make responsible decisions; we make responsible commitments; and we take responsible actions.
Team
We work together as one team either on individual project or the whole company. Team spirit is our core value. We work hard, we play hard. We support and help each other to achieve our goals and grow personally and professionally. We respect and trust each other. We don’t let our work mates down.
Innovation
We live by and for innovation. We encourage and nourish the spirit of innovation in all aspects of our company’s development. We love challenges, as well as improvements. We convert the cutting-edge of our innovation into our customers’ competitiveness.
History of USEON Innovations
Manufactured SAT360 The largest extruder ever annual throughput of 400,000 KTA.
Delivered the SAT150 extruder for lithium battery separator film, exported the SAT175 extruder for lithium battery separator film to France.
We have manufactured advanced energy saving, lightweight, environmental-friendly micro-foamed PET sheet; we launched our industry-leading PET / PLA micro-foamed sheet production line.
The global COVID-19 pandemic was raging, and mask-related equipment was urgently needed. The melt blown fabric equipment developed by Useon were exported to Canada, Germany, the UK, India and other places. In addition, the domestically produced XPS production line with the highest output of 2000kg/h was delivered, and we successfully helped European XPS customers commission their XPS line by remote technical support system.
Delivered the first XPET production line.
Delivered PE/PP compounding jumbo extruder SAT-X175, the throughput is 8-10 tons / h.
Delivered the first PLA foam beads production line.
Developed our solution for PET foam board extrusion, used in applications such as, wind power, rail traffic, aviation, and decoration.
Launched a triple-screw extruder with superior dispersion and distribution capability for POY / BSF MB and TPU reaction mixing and put into operation.
Developed high-efficiency heating and dual-channel cooling barrels for twin-screw extruders, along with a high-precision temperature control system.
Launched high-torque gearbox with torque density of 13Nm/cm3 for twin screw extruder.
We launched our New Product, Graphite EPS Pelletizing Line.
We implemented a UNIDO HCFC replacement plan.
We improved the line speed of EVA solar cell encapsulating film up to 10m/min.
We delivered the first set of China-made twin screw extruders for BOPET which eliminated the pre-dry process. This offered energy savings up to 35%.
We increased the speed of our high torque twin screw extruder up to 800rpm.
Following our achievements of 2008 we set out to deliver the first set of EVA solar cell encapulating film. We completed a complete production line with a twin screw extruder.
2009 also saw us realize our goal of delivering a 1000kg/hr, CO2 foam XPS production line.
We achieved two milestones in 2008!
Firstly, we developed pre-dry-free PET extrusion technology for use in our twin-screw extruder.
Then we launched first set of twin-screw extruders with a single screw extruder tandem extrusion line for CO2 foam XPS production.