Devolatilization
The screw-type continuous reaction devolatilization technology developed by USEON is an advanced process solution in the field of polymer material processing, focusing on efficiently removing solvents and impurities from materials and applicable to a wide solvent content range from 5% to 85%.
This technology has been widely applied in the solvent devolatilization processes of polymers such as POE (polyolefin elastomer), PMMA (polymethyl methacrylate), COC (cyclic olefin copolymer), and α-olefins, offering significant process advantages.
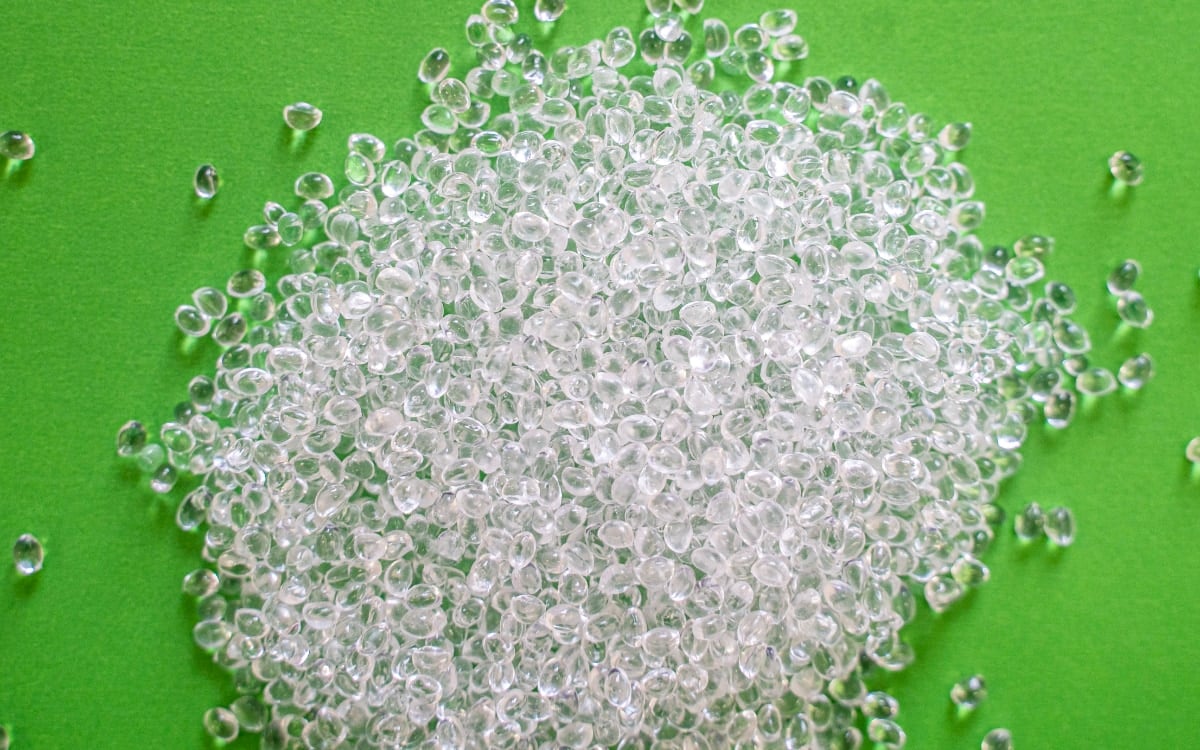
Table of Contents
Professional Practice
USEON has extensive experience in screw-type continuous reaction devolatilization technology, particularly for devolatilizing POE systems with high solvent ratios. With its proprietary “controlled stepwise devolatilization process” technology, USEON can efficiently remove 50%–75% of solvent content directly within the twin-screw extruder, reducing residual solvent levels to 50–200 ppm. This precise process control significantly enhances devolatilization efficiency and production output, meeting stringent purity standards.
Main Devolatilization Modes
1. Flash Devolatilization Mode
By heating to instantly vaporize the solvent, the flash effect is utilized to quickly and efficiently remove the solvent, making it especially suitable for the removal of high-boiling or low-volatility solvents, ensuring high devolatilization efficiency.
2. Surface Renewal Mode
In the continuous desolvation process, the surface of the material is continuously refreshed to accelerate the evaporation of the solvent. This mode is particularly suitable for processing materials with high solvent content, enhancing the overall desolvation efficiency.
3. Foaming Mode
By controlling the process parameters to achieve micro-foaming of the material, the solvent and impurities are effectively separated during the foaming process, further optimizing the stripping effect. This mode is especially suitable for the special stripping needs of certain specific polymer materials.
Technical Advantages
Polymer Continuous Reaction
In the devolatilization process, it supports continuous polymerization reactions, making production more efficient. This feature reduces the redundancy of traditional multi-step reactions, enhancing production stability and continuity.
Online Compounding
USEON’s screw extruder-based continuous reaction devolatilization technology can complete the mixing of raw materials and additives during the processing, enhancing the flexibility and efficiency of the production process, meeting various formulation requirements, and saving additional mixing steps.
High-Efficiency Devolatilization
The technology can effectively remove impurities and solvents with various boiling points, from high boiling point impurities to low boiling point solvents, ensuring the high purity and quality of the products. Products that have undergone high-efficiency devolatilization have lower residual solvent levels, meeting strict environmental and safety standards.
Equipment Selection
USEON’s screw-type continuous reaction devolatilization technology provides an excellent process solution for the efficient devolatilization and high-quality preparation of polymer materials. With extensive experimental and application experience, it is an essential guarantee for stable, efficient, and safe production in the industry.
Our SAT series twin screw extruder can fully meet your needs in devolatilization applications. Please feel free to contact us for further discussions.