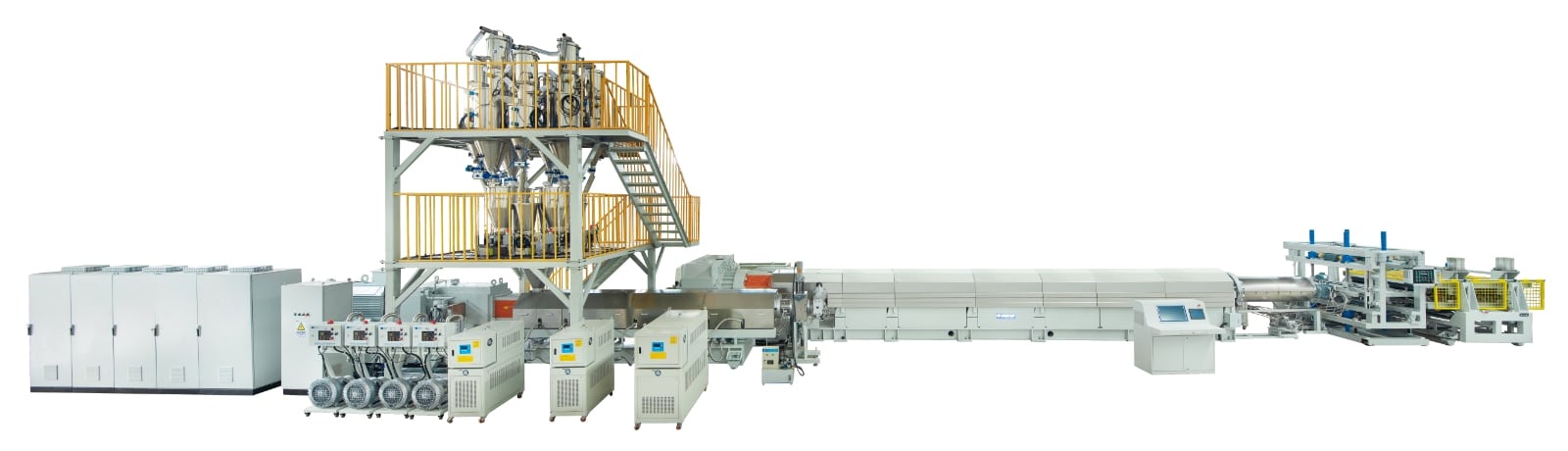
CO2 Foam XPS Production Line
Our ECOFEL series XPS line represents the most advanced domestically manufactured XPS production line. With our help, we have helped launch numerous XPS production facilities for international companies.
Our vast experience and cooperation with international companies ensures you a world-class XPS factory and greater competitive advantage, while promising service and quality. Don’t hesitate to contact us today and consult with one of our experts.
USEON Clients
Successfully supplied 300+ XPS Foam Board Production Lines to multiple countries globally
Why Choose USEON XPS Lines
Many Leading Companies Trust Our Products
USEON is leading the extruded polystyrene machine market in China, and we have worked with and provided machinery to countless well-known international companies, such as BASF, Owens Corning, ISOFOAM, Ravago, and more. We are also trusted and recognized by organizations of the United Nations.
Save 40% on Your Investment
Our machinery qualifies for international quality and safety standards and is offered at a much more affordable price. Typically, we can help you save 40% of the cost, compared to other European suppliers. We will ensure you with both satisfied products and service from our expert team and multilingual service team.
Over 300 XPS Foam Board Lines Launched
To date, we have launched and delivered over 300 foam XPS extrusion lines to countries all over the world including Australia, South Korea, Saudi Arabia, Kuwait, Romania, Turkey, and more. Our number of consumers and locations continue to expand across the world, and we are confident that our rich experience will ensure you satisfaction in what we do.
Latest Technology
Innovation is one of our core values; work with us, and we will keep you at the cutting edge of XPS technology.
Turn-key Project
Inclusive of feasibility studies, staff training, and production planning, we provide a full menu of services covering all important aspects of your project. Our professional team will be with you all the way.
Technical Support and Service
Our experts and engineers are here to assist and guide you to solutions for challenges that you face and to optimize production performance. Through our operation of the new DCS intelligent control system, we provide effortless, remote, synchronized, and accurate technical support.
ECOFEL propels the technology of extruded polystyrene CO2 foam production that holds tremendous future potential. We are eager and committed to implementing you a greener XPS production with sustainable advantages. We do not only deliver high-performance and reliable machines, but we also focus on sharing our expertise on producing excellent quality foam boards.
Through close cooperation with our customers, we design our machines for optimum processing performance and engineering capability, facilitating work for the manufacturing team.
From 20mm to 150mm in thickness, from 600mm to 1200mm in width, from 200kg/hr to 3000kg/hr throughput, USEON provides an extensive range of production lines, allowing you to match your requirements to the exact machine performance.
Table of Contents
USEON ECOFEL Series Key Features
- Leading XPS Production Line Manufacturer in China
- Successfully supplied 300 XPS Foam Board Production Lines to multiple countries globally
- Achieve outputs of up to 3,000 kg/h
- Produce XPS Board width between 450mm and 1250mm
ECOFEL Series Machine Models
Model | Throughput (kg/h) | Transformer Required |
---|---|---|
TDS75-TDD150 | 200~450 | 300 KVA |
TDS75-TDD200 | 400~600 | 400 KVA |
TDS95-TDD250 | 600~1000 | 500 KVA |
TDS110-TDD300 | 800~1200 | 600 KVA |
TDS135-TDD400 | 1500~2000 | 800 KVA |
TDS135-TDD500 | 2000~3000 | 1200 KVA |
Layout of XPS Line
The layout of different models is almost the same. We will also make some minor adjustments to the layout according to your plant situation.
Excellent Quality and Reliability
The quality and reliability of ECOFELTM is recognized by Fortune 500 groups, and leading worldwide XPS manufacturers. This includes UNIDO (United Nations Industrial Development Organization), Owens Corning.
As a strategic partner of UNIDO and their quest to phase-out the usage of HCFCs in XPS production, USEON is providing global support for multiple projects.
Fully Automatic Raw Material Handling System
Continuous and uniform feeding is a key step in producing excellent products. All recipe changes can be done using digital settings. Incorporated with our DCS intelligent control system, it manages production parameters and controls cost more effectively.
Our integrated vacuum loading system and raw material handling solutions can be customized according to individual factory circumstances. This ensures excellent housekeeping and a clean environment throughout the facility.
TDS-D High Torque Twin Screw Extruder
In comparison to typical domestically produced compounding twin screw extruders, our extruders are very different, as we adopt TDS-D series high torque, which brings the specific torque of our extruders up to 10.3 Nm/cm3.
Our high torque twin screw extruders offer many advantages as follows:
- Maintain the lowest possible melt temperature during processing
- Minimize the usage of flame retardant additive whilst maintaining the same flame retardancy level
- Keep the colour of the product bright and fresh
- Excellent for producing high compressive strength boards
Highly modularized barrels and screws as well as blowing agent injection flange allow TDS-D twin screw extruders to have wider flexibility and suitability. All CNC manufactured barrels and screws assure the precise fit, providing excellent mixing and dispersion as well as optimum residence time distribution (RTD). This all saves additive usage, in addition to enhancing product quality.
Innovative Cooling Single Screw Extruder
Temperature control is extremely important when extruding foam. The innovative barrel design of our latest single screw extruder has increased cooling capacity by 80% compared with traditional designs.
In addition to our super cooled barrel design, our latest screw profile increases renewal rate of molten materials, ensuring the cooling efficiency and homogenization of the polymer, yet decreasing the power consumption by 30%.
Blowing Agent System
Strike the Balance Between Cost and Quality.
Variable physical properties of CO2 make accurate metering a challenge. It involves temperature and pressure control, mass flow rate control, and a fine balance between processing parameters.
We have designed a CO2 system which controls all the key parameters, to ensure precise metering. Our multiple blowing agent injection system allows you to shift the product portfolio easily, quickly adjusting to suit different market conditions. This also assures constant quality and cost control, therefore maximizing your profit margins.
Downstream
We provide complete downstream systems, including calibrator, haul-off, edge trimming, cut-off, stacker, and auto-packaging system. We customize the downstream system according to customer requirements, also adapting to existing building. Surface planner, surface groover, embossing, shiplap edge, and tongue & groove edge accessories can be online or offline to suit the product being produced.
DCS Intelligent Control System
A Prelude to Industry 4.0. Pulling data from recipe management and operation history, then optimizing the parameters using big data. Extracting data from maintenance records and alarm history, remote analysis and technical support can easily be done through such notifications.
DCS intelligent control system helps you manage your production and maintain your equipment more effectively. Powerful industry PC leads your XPS production into the Big Data Era.
Turn-key Projects
To operate successful XPS projects, selecting high-quality equipment is the first step; however, at USEON, we offer so much more. Our professional team do not only provide the best equipment, but also extensive services. These cover workshop design consulting, warehouse logistic management, recipe management operation, and maintenance training.
We achieve this with the help of our diverse expert team and services and supply well-rounded, precise, and comprehensive solutions.
XPS Foam Board Applications
Our ECOFELTM Series XPS production line produces high quality XPS Foam Board for many applications.
Insulation
– Energy-saving for building
– Pipe insulation
– High-speed railway track
High Compressive Strength
– Foundations of airport runways, Roadways
– Under slab, concrete floors
– Safety barriers
Other Potential Applications
– Aeroponics system
– Ceiling decoration
– Composited panels
Updates of USEON
XPS Extrusion Projects
Guides for XPS Production
How to Control Your CO2 in XPS Production Line
For end customers, knowing this information would not get you anywhere. You still need reliable design to warranty the productivity of your production line.
How to Configure Your XPS Production Line
Before your investment, you need to learn something about how to configure your XPS production line to get the most out of your investment.
How to Figure Out the Portfolio of Blowing Agents for XPS Production
In this article, we are going to tell you something about how to figure out the portfolio of the blowing agents for XPS production.
How to Recycle XPS Foam
In this guide, you’ll learn 3 recycling method of waste Polystyrene (XPS/EPS foam). USEON can provide complete XPS recycling solutions. You can choose water ring pelletizing system or water cooling strand pelletizing system.
FAQs
Our TDS135-TDD500 can yield 3,000kg/hr.
ECOFEL series XPS foam board machine can work with CO2, ethanol, DME, HFC, HFO, butane, pentane and LPG etc. Usually the portfolio of different blow agents is recommended to reach the balance of product cost, easy operation and thermal conductivity.
We can guarantee the lowest density of 25kg/m3, and highest density of 50kg/m3. However, we have clients can make it lower than 25kg/m3 and higher than 50kg/m3.
Our XPS machine is able to produce the compressive strength more than 1,000KPA.
Our full series of lines can produce from 10-200mm thickness directly. However, each model has its own suitable range, therefore thickness range of targeting market is the key determining factor when selecting machine.
The international standard width is 600mm, some countries have 1200mm and 900mm width. In principle, any width can be produced by changing die or adding slitting machine.
The thermal conductivity (lambda value) falls between 0.024-0.038 W/(m·K), depends on the recipe of solid raw materials, portfolio of blowing agents, as well as thickness of the boards.
Yes, this line has to work 24 hours. Because every start-up will take a couple of hours to heat up and waste at least one hour of scrap.
It varies from model to model.
Generally, 70m x 8m x 8m is the minimum requirement for production line only. Minimum 2,000sqm is required for the whole plant.
The number of personnel required for each production line varies based on its output and whether it is equipped with an automatic packaging machine.
Model: TDS75-TDD150
Positions | Person with Automatic Packaging | Person without Automatic Packaging |
---|---|---|
Feeding & Forklift Operator | 1*2 | 1*2 |
Machine Monitoring | 1*2 | 1*2 |
Crosscut & Milling Operator | 1*2 | 1*2 |
Packing Operator | / | 2*2 |
Palletizing & Forklift Operator | 1*2 | 1*2 |
Granulation and Regrind Operator | 2 | 2 |
Main Machine Operator | 1 | 1 |
Mechanic and Electrician | 2 | 2 |
Total Person | 13 | 17 |
Model: TDS135-TDD400
Positions | Person with Automatic Packaging | Person without Automatic Packaging |
---|---|---|
Feeding & Forklift Operator | 1*2 | 1*2 |
Machine Monitoring | 1*2 | 1*2 |
Crosscut & Milling Operator | 2*2 | 2*2 |
Packing Operator | / | 2*2 |
Palletizing & Forklift Operator | 1*2 | 1*2 |
Granulation and Regrind Operator | 3 | 3 |
Main Machine Operator | 1 | 1 |
Mechanic and Electrician | 2 | 2 |
Total Person | 16 | 20 |
Typically, if you don't opt for automated packaging equipment, you'll need an additional 4 workers to ensure the smooth operation of the production line.
Here is a brief introduction to these positions:
- Feeding & Forklift Operator: Transports raw materials to the feed bin, he needs to know how to operate a forklift.
- Machine Monitoring: Monitors the operational status of the main machine and performs basic operations.
- Crosscut & Milling Operator: Controls the stability of XPS boards dimensions.
- Packing Operator: Manually packs products in the absence of an automatic packaging machine.
- Palletizing & Forklift Operator: Stacks and arranges finished products neatly into the finished goods warehouse.
- Granulation and Regrind Operator: Processes waste and trimmed materials during production into granules for reuse.
- Main Machine Operator: Adjusts system parameters when changing product specifications.
- Mechanic and Electrician: Maintains and repairs machinery to ensure the smooth operation of the production line.
Yes, we do.
We provide 10-100kg/hr lab line for foam extrusion. The final product can be sheet, board or beads.
Absolutely. We offer both complete production lines and individual functional units to enhance your existing production lines. Available units include the blowing agent dosing system, cut-off machine, edge trimmer, haul-off machine, stacker, packaging machine, and more.
Please consult with our expert; sometimes a small change can lead to significant improvements.
Our XPS foam line has been sold to many countries around the world and has helped our customers successfully put into production more than 300 production lines.
These countries are mainly as follows:
- Australia
- Azerbaijan
- Brazil
- China
- Egypt
- Georgia
- Hungary
- India
- Kazakhstan
- Kosovo
- Kuwait
- Malaysia
- Moldova
- Morocco
- Oman
- Pakistan
- Poland
- Qatar
- Romania
- Saudi Arabia
- South Korea
- Turkey
- Ukraine
- United Arab Emirates
- United Kingdom
- United States
- Uzbekistan
- Vietnam