This article provides a comprehensive introduction to the basic knowledge, classification, processing techniques of polyethylene (PE), as well as the challenges it faces in development and its future development trends. It thoroughly discusses the different types of PE, such as LDPE, LLDPE, MDPE, HDPE, and UHMWPE, and analyzes their chemical stability, processing advantages, and challenges in recycling and environmental sustainability. At the same time, it looks forward to the potential development directions of PE in terms of technological innovation, market demand, environmental policies, and global competition.
What is Polyethylene (PE)?
Polyethylene (PE) is a thermoplastic resin made by polymerizing ethylene, with the chemical formula (C2H4)n.
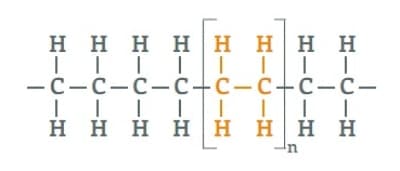
Part 1: Basic Knowledge of Polyethylene
1. Basic Knowledge of Polyethylene
Polyethylene is odorless, non-toxic, and feels like wax. PE resins for molding and processing are waxy pellets obtained through extrusion and granulation, appearing milky white.
The molecular weight ranges from 10,000 to 1,000,000. Ultra-high molecular weight polyethylene has a molecular weight exceeding 100,000. The higher the molecular weight, the better the physical and mechanical properties, approaching the requirements of engineering materials. However, the higher the molecular weight, the more difficult the processing.
Polyethylene has a melting point of 100-130°C and excellent low-temperature resistance, maintaining good mechanical properties even at -60°C.
Polyethylene has good chemical stability and can resist dilute nitric acid, dilute sulfuric acid, and any concentration of hydrochloric acid, hydrofluoric acid, phosphoric acid, formic acid, acetic acid, ammonia water, amines, hydrogen peroxide, sodium hydroxide, and potassium hydroxide solutions at room temperature. However, it is not resistant to strong oxidative corrosion, such as fuming sulfuric acid, concentrated nitric acid, and mixtures of chromic acid and sulfuric acid. These solvents can slowly corrode polyethylene at room temperature, while concentrated sulfuric acid and concentrated nitric acid can rapidly corrode polyethylene at 90-100°C, causing destruction or decomposition.
Polyethylene will age, discolor, crack, become brittle, or powder and lose its mechanical properties when exposed to the atmosphere, sunlight, and oxygen. At molding and processing temperatures, oxidation can also reduce the melt viscosity, causing discoloration and streaks. Therefore, attention should be paid to oxidation during molding, processing, and material selection. Due to these properties, polyethylene is easy to process and mold, making its recycling and reuse very valuable.
Plastics with recycling codes 2 and 4 in daily life are made of PE, which have different crystal structures.
2. Classification of Polyethylene
Polyethylene can be divided into several main types based on its density and molecular structure:
Low-Density Polyethylene (LDPE)
Structure and Characteristics: LDPE has a more branched structure and a looser molecular chain, resulting in lower density (0.910–0.925 g/cm³). This structure gives it good flexibility, transparency, and impact resistance, but poor mechanical strength and heat resistance.
Applications: LDPE is widely used in films, food packaging bags, plastic bags, extrusion coatings, and insulation layers for wires and cables.
Linear Low-Density Polyethylene (LLDPE)
Structure and Characteristics: LLDPE is produced by copolymerization, with a linear molecular structure and short branches, with a density between 0.915–0.940 g/cm³. Compared with LDPE, LLDPE has higher tensile strength and puncture resistance while maintaining good flexibility and transparency.
Applications: LLDPE is commonly used to make films, agricultural films, packaging films, and sheaths for wires and cables.
Medium-Density Polyethylene (MDPE)
Structure and Characteristics: MDPE has a density between 0.926–0.940 g/cm³, with properties between LDPE and HDPE, having good impact resistance and chemical corrosion resistance.
Applications: MDPE is mainly used for pipes, films, and injection-molded products.
High-Density Polyethylene (HDPE)
Structure and Characteristics: HDPE has a linear structure with few branches, resulting in higher density (0.941–0.965 g/cm³). This structure gives it excellent mechanical strength, chemical resistance, and heat resistance but poor flexibility and transparency.
Applications: HDPE is widely used in making pipes, bottles, barrels, films, plastic toys, and household appliance casings.
HDPE serves as the outer layer material in 3LPE coatings, primarily providing physical protection and corrosion resistance for pipelines. It offers excellent wear resistance, impact resistance, and chemical corrosion resistance, effectively preventing external mechanical damage and environmental corrosion, thereby extending the pipeline’s service life. It is widely used in the external protection of pipelines transporting oil, gas, and water. USEON can provide high-quality HDPE compounding and pelletizing solutions, ensuring material quality and performance stability during the production process.
Ultra-High Molecular Weight Polyethylene (UHMWPE)
Structure and Characteristics: UHMWPE has a very high molecular weight (usually between 1.5 million and 7 million), exhibiting extremely high wear resistance, impact resistance, and self-lubricating properties, with a very low coefficient of friction.
Applications:
1). Aeronautics and National Defense:
– Bulletproof vests and helmets: UHMWPE fibers are one of the main materials for manufacturing bulletproof equipment, providing lightweight and efficient protection.
– Internal components of aircraft and spacecraft: Utilizing its lightweight, wear resistance, and impact resistance.
2). Petrochemical and Energy Industry:
– Pipelines and valves: UHMWPE piping is used for transporting corrosive fluids, such as crude oil and chemicals.
– Separator membranes: Used in lithium-ion batteries to provide a safe ion channel and prevent short circuits.
3). Automotive Manufacturing:
– Interior materials: Used for shock absorption, sound insulation, and wear-resistant parts.
– Battery separators: Used in the battery packs of electric vehicles.
4). Sports and Recreation:
– Safety helmets, snowboards, sailcloths, etc., leveraging their strength and lightweight characteristics.
5). Mining and Quarrying:
– Conveyor belts, liners, chutes, etc., to reduce wear and extend equipment life.
6). Marine Engineering:
– Ropes and cables: Used for mooring and towing of vessels, offering high strength and lightweight.
The applications of UHMWPE are continuously expanding. With the advancement of material science, new types of UHMWPE materials and composites are being developed to meet more demanding environmental requirements and specific performance needs.
Ethylene-Vinyl Acetate Copolymer (EVA)
Structure and Characteristics: EVA is a copolymer of ethylene and vinyl acetate monomers, with good flexibility, elasticity, and transparency. The higher the vinyl acetate content, the better the softness and elasticity of the material, but the strength and heat resistance decrease.
Applications: EVA is mainly used in shoe materials, toys, soft packaging films, hot melt adhesives, and cable sheaths.
Cross-Linked Polyethylene (PEX / XLPE)
Polyethylene molecules are cross-linked to form a network structure through chemical or physical methods, providing higher temperature and pressure resistance, commonly used in hot water pipes and underfloor heating pipes, cables.
Although both PEX and XLPE are cross-linked polyethylenes, they are not the same. The specific differences can be found in the FAQs at the end of this document.
High-Pressure Polyethylene (HPPE)
HPPE is produced by high-pressure polymerization, mainly used in films and container products.
Part 2: Polyethylene Processing
There are various processing techniques for polyethylene, depending on the final product’s intended use and form. The most common processing techniques include the following:
1. Compounding and Pelletizing
Principle: Polyethylene is mixed with other additives (such as plasticizers, stabilizers, fillers, etc.) in an extruder. The mixture is melted, extruded, and then cut into pellets.
Applications: Produces polyethylene pellets with specific properties and uses, suitable for various subsequent processing techniques.
Advantages: The performance of polyethylene can be adjusted by adding different additives and modifiers, meeting the needs of different application areas.
USEON has delivered over 2,500 twin screw extruders, featuring 5 major series of twin screw extruders, covering uses from laboratory purposes to mass production, with output ranges from 5kg/h to 60t/h.
2. Extrusion Molding
Principle: In extrusion molding, polyethylene raw materials in the form of pellets or powder are mixed with necessary additives and colorants, heated to a molten state in an extruder, and impurities are removed through a filter. The molten plastic is then extruded through a die to form the desired shape. Twin-screw extruders are particularly suitable for processing PE due to their strong mixing and plasticizing capabilities.
Applications: Pipes, films, sheets, cable sheaths, etc.
3. Injection Molding
Principle: Polyethylene is heated to a molten state and then injected into a mold under high pressure to cool and solidify, forming complex-shaped products.
Applications: Toys, household appliance casings, bottle caps, containers, etc.
4. Blow Molding
Principle: A polyethylene melt is made into a parison, which is then inflated with gas pressure to conform to the mold’s inner wall, cooling and solidifying into shape.
Applications: Hollow containers, such as plastic bottles, barrels, fuel tanks, etc.
5. Rotational Molding
Principle: Polyethylene powder is added to a mold, which rotates along two vertical axes and is heated. The powder melts and evenly distributes along the mold’s inner wall, forming hollow products upon cooling.
Applications: Large hollow products such as water storage tanks, children’s toys, kayaks, etc.
6. Calendering
Principle: Polyethylene melt is passed through multiple calendering rollers to press it into films or sheets of specific thickness.
Applications: Films, sheets, flooring materials, etc.
7. Thermoforming
Principle: Polyethylene sheets are heated to soften, then formed against the mold surface using vacuum or pressure, and cooled to solidify.
Applications: Food packaging boxes, trays, containers, etc.
8. Foam Molding
Principle: A foaming agent is added to polyethylene, and through chemical or physical methods, the material forms a porous structure to create lightweight materials.
Applications: Insulation materials, cushioning packaging materials, shoe materials, etc.
9. Blown Film Foaming
Principle: Combining extrusion blown film processes with foaming technology to produce films with foam structures.
Applications: Insulating packaging materials, soundproofing materials, etc.
10. Hot Melt Adhesive Processing
Principle: Polyethylene is mixed with other components to produce hot melt adhesives, which are heated and melted to coat or dip on substrate surfaces.
Applications: Packaging seals, labels, carpet backing, etc.
Part 3: Challenges Faced by Polyethylene
Polyethylene (PE), as a widely used synthetic resin, faces various challenges in its development process:
- Overcapacity: With the rapid expansion of polyethylene production capacity, the market may face the problem of oversupply, which could lead to intensified price competition, affecting the profitability of enterprises.
- Product homogenization: Polyethylene products exhibit homogenization in some areas, making it difficult for companies to gain a competitive advantage through product differentiation, increasing the difficulty of market competition.
- Raw material price fluctuations: The production cost of polyethylene is greatly influenced by the volatility of crude oil prices. The uncertainty of crude oil prices poses challenges for polyethylene production enterprises in terms of cost control.
- Need for technological innovation: To improve product performance and reduce production costs, the polyethylene industry needs to continuously innovate in technology, including the development of new catalysts and the improvement of production processes.
- Environmental and sustainability pressures: With the global emphasis on environmental protection and sustainable development, the polyethylene industry faces challenges in improving the recyclability of materials and reducing environmental impact.
- Changes in the international trade environment: The uncertainty of the global trade environment, such as trade frictions and changes in tariff policies, may affect the international trade and market access of polyethylene products.
- Competition from alternative materials: Other types of plastics or bio-based materials may become substitutes for polyethylene, requiring the polyethylene industry to enhance the competitiveness of its products.
- Growing demand for high-end products: The market’s demand for high-performance polyethylene materials is increasing, requiring companies to improve product quality to meet the needs of the high-end market.
- Industrial chain integration: To improve efficiency and reduce costs, the polyethylene industry needs to integrate the industrial chain, including expansion into upstream raw material supply and downstream application fields.
Part 4: Future Development Trends of Polyethylene
The future development trends of the polyethylene (PE) industry can be observed and analyzed from multiple perspectives, with some main trends as follows:
- Product diversification and high performance: With technological advancements, polyethylene products will develop towards diversification and high performance to meet the needs of various application fields. For example, ultra-high molecular weight polyethylene (UHMWPE) is valued for its outstanding performance.
- Technological innovation in production processes: Polyethylene production technology will continue to be optimized and innovated, including progress in catalyst technology and improvements in polymerization processes, to enhance production efficiency and product quality.
- Environmental protection and sustainability: Environmental protection and sustainability have become key directions for the development of the polyethylene industry. The future will focus more on using renewable resources, reducing waste and energy consumption, and reducing environmental impact.
- Digital manufacturing: The application of digital technology, especially 3D printing technology, in polyethylene production will increase, which helps to improve production efficiency and achieve personalized manufacturing.
- Industrial chain integration: To improve efficiency and reduce costs, the polyethylene industry will strengthen the integration of the industrial chain, including expansion into upstream raw material supply and downstream application fields.
- Intense market competition: With the rapid growth of production capacity, the polyethylene market will face more intense competition, especially in the field of general products.
- Competition from alternative materials: Faced with competition from other plastics or bio-based materials, the polyethylene industry needs to continuously enhance the competitiveness of its products.
- Growing demand for high-end products: The market demand for high-end polyethylene materials will continue to grow, driving companies to improve product quality and develop new application areas.
- Concentrated capacity deployment: It is expected that in the next few years, the domestic polyethylene industry will enter a period of concentrated capacity deployment, and the new production capacity will have an impact on the market supply and demand balance.
The polyethylene (PE) industry has great development potential and opportunities while facing challenges.
FAQs
Polyethylene is a non-toxic, odorless material widely used in food and medical packaging, with high safety.
Depending on the specific application, it generally ranges from 10 to 50 years.
While both PEX (Cross-linked Polyethylene) and XLPE (Chemically Cross-linked Polyethylene) enhance the thermal stability and mechanical properties of polyethylene through cross-linking, there are some key differences between them:
1. Cross-linking Method: PEX can be produced through chemical methods (such as peroxide cross-linking) or physical methods (such as radiation cross-linking), whereas XLPE is typically cross-linked using chemical cross-linking agents at high temperatures.
2. Application Areas: PEX is mainly used in piping systems, especially for potable water and radiant heating applications, due to its excellent pressure and temperature resistance. XLPE, on the other hand, is primarily used as an insulating material for electrical wires and cables, known for its superior electrical insulation and heat resistance.
3. Performance Characteristics: Although both improve the heat resistance and mechanical strength of polyethylene, XLPE exhibits higher temperature ratings and better electrical insulation properties for electrical applications.
The choice between PEX and XLPE usually depends on the specific application requirements and performance standards of the end product.
Waste polyethylene can be treated through mechanical recycling, chemical recycling, and energy recovery methods to reduce environmental impact.
Polyethylene has good heat and cold resistance. Generally, LDPE's heat resistance temperature is around 80°C, while HDPE can withstand temperatures up to 120°C. Polyethylene maintains good flexibility and impact strength at low temperatures.
Polyethylene itself is non-degradable and can cause plastic pollution if it persists in the environment for a long time. However, recycling and developing bio-based polyethylene can reduce its environmental impact. Developing degradable polyethylene materials is also an important future direction.
Polyethylene has excellent mechanical properties, including good impact resistance, wear resistance, and chemical corrosion resistance. HDPE has higher strength and rigidity, while LDPE and LLDPE offer better flexibility and transparency.
Polyethylene differs from other common plastics (such as polypropylene, polyvinyl chloride, polystyrene, etc.) in chemical structure, performance, and application. Polyethylene has good chemical stability and a wide range of applications, but its heat resistance and mechanical strength may be inferior to other plastics in some aspects.