What is Polystyrene (PS)?
Polystyrene (PS) is a polymer synthesized through the free radical polymerization of styrene monomers, and it is a colorless, transparent thermoplastic.
In the plastic resin identification coding system, PS is designated by the number 6 (a triangular chasing-arrows symbol with the digit inside). This code must be clearly marked on the bottom of the plastic product or its packaging to facilitate proper sorting by consumers and recyclers.
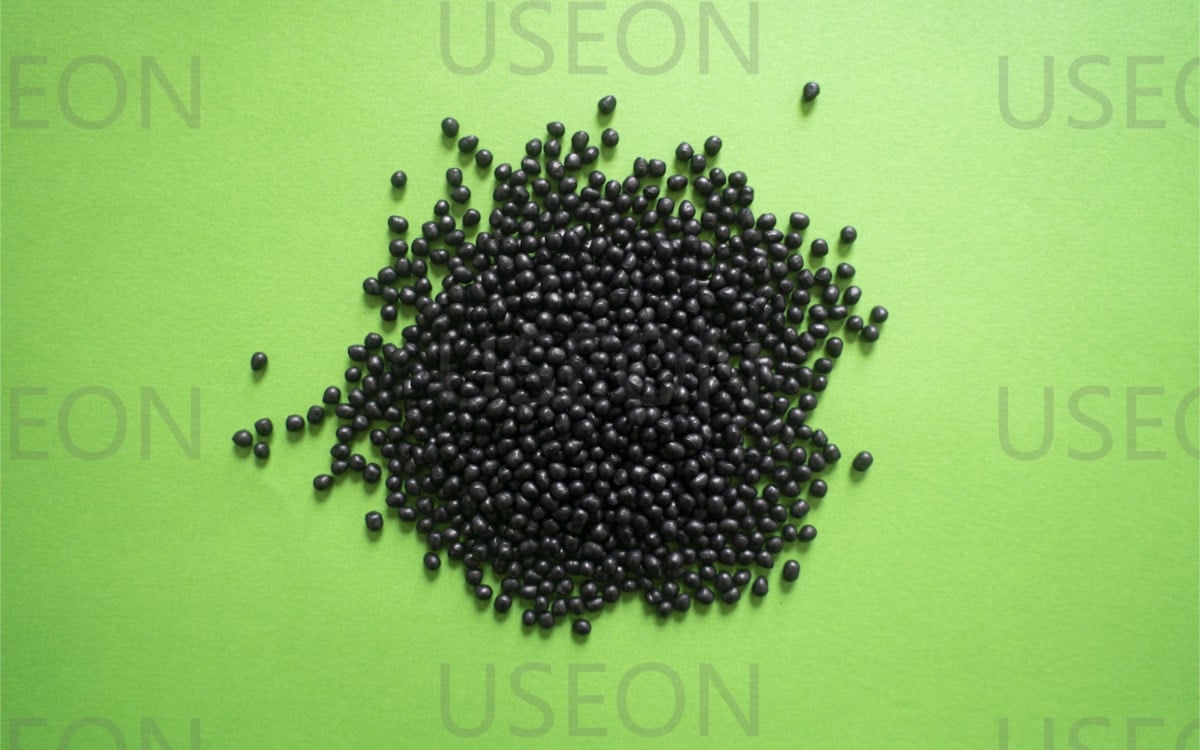
Part 1: Basic Knowledge of Polystyrene (PS)
Physical Properties
PS appears as colorless, transparent pellets. When burned, it emits thick smoke with a turpentine-like odor, and the flame produces long, drawn-out strands when blown out. PS products are rigid and glass-like, producing a metallic sound when dropped or struck. They are brittle rather than flexible, and the fracture surface exhibits a pearly, silvery sheen. PS has a water absorption rate of 0.05%, slightly higher than PE, but this has minimal impact on the strength and dimensional stability of the product.
Optical Properties
Excellent transparency is one of PS’s most notable characteristics, with a light transmittance of 88%–92%. Along with PC and PMMA, PS is considered one of the top three transparent plastics in the market.
Mechanical Properties
PS is hard and brittle, lacking ductility—it fractures near the yield point under tension. Among general-purpose thermoplastics, PS has the highest tensile and flexural strength, with tensile strength reaching up to 60 MPa. However, its impact strength is very low, making it unsuitable for engineering plastics. PS has poor wear resistance and moderate creep resistance. Its mechanical properties are highly temperature-dependent.
Thermal Properties
PS has poor heat resistance, with a heat deflection temperature of only 70–90°C, limiting its long-term use to temperatures between 60–80°C. It also performs poorly at low temperatures, with a brittle point of -30°C.
Electrical Properties
PS exhibits excellent electrical insulation properties, unaffected by temperature or humidity. It has a low dielectric loss tangent, can withstand moderate corona discharge, and has good arc resistance, making it suitable for high-frequency insulating materials.
Chemical Resistance
PS has good chemical stability, resisting weak acids, alkalis, salts, mineral oils, and lower alcohols. However, it is susceptible to attack by many hydrocarbons, ketones, and higher fatty acids, and dissolves in aromatic solvents. PS has poor weatherability, with low resistance to light and oxidation, making it unsuitable for long-term outdoor use. However, it has good radiation resistance.
Part 2: Types of Polystyrene (PS)
Polystyrene (PS) can be mainly classified into the following types based on its characteristics and applications:
1. General Purpose Polystyrene (GPPS)
Characteristics: Also known as general-purpose polystyrene, it has good transparency, rigidity, and electrical insulation properties.
Applications: Widely used in the production of transparent plastic products such as food containers, CD cases, test tubes, stationery, and decorative materials.
2. High Impact Polystyrene (HIPS)
Characteristics: Rubber (usually styrene-butadiene rubber) is added to general-purpose polystyrene to enhance its impact resistance and toughness; it is usually milky white or opaque.
Applications: Suitable for products requiring higher strength and toughness, such as appliance housings, toys, instrument casings, and refrigerator liners.
3. Expanded Polystyrene (EPS)
Characteristics: Produced through a foaming process, it features light weight, thermal insulation, and cushioning properties.
Applications: Used in the production of insulation materials, packaging materials, disposable tableware, and thermal insulation panels for construction.
4. Extruded Polystyrene (XPS)
Characteristics: Also a type of expanded polystyrene, but produced by extrusion foaming, forming a uniform closed-cell structure with higher compressive strength and better thermal insulation.
Applications: Commonly used in building insulation systems, cold storage insulation, and floor insulation.
5. Degradable Polystyrene
Characteristics: Degradation agents are added to general-purpose polystyrene to make it more environmentally degradable, reducing its environmental impact.
Applications: Used for eco-friendly packaging materials and disposable products.
6. Anti-static Polystyrene
Characteristics: Anti-static agents are added to polystyrene to reduce the buildup of static electricity.
Applications: Used in electronic product packaging and other applications requiring anti-static properties.
These types of polystyrene differ significantly in performance and applications, meeting various usage requirements.
Part 3: Applications of Polystyrene (PS)
PS materials have a wide range of applications, which can generally be categorized into the following fields:
1. Pharmaceutical Industry
Pharmaceutical wastewater mainly includes four categories: wastewater from antibiotic production, synthetic drug production, traditional Chinese medicine production, and washing/rinsing wastewater from various formulation processes. This type of wastewater is characterized by complex composition, high organic content, high toxicity, deep color, and high salinity. It is particularly difficult to treat due to its poor biodegradability and intermittent discharge, making it a challenging type of industrial wastewater.
Moreover, due to its complex composition, pharmaceutical wastewater is highly corrosive, requiring strong corrosion resistance from treatment facilities. The organic components in the water can corrode commonly used resin-based anti-corrosion coatings, significantly shortening the service life of the equipment.
PS material is highly resistant to high concentrations of acids, alkalis, salts, oils, and most solvents, making it very suitable for harsh environments like pharmaceutical wastewater with complex and corrosive compositions.
2. Chlor-alkali Industry
The chlor-alkali industry primarily consists of two major parts: the electrolysis of brine to produce sodium hydroxide, chlorine, and hydrogen, and the polymerization of vinyl chloride monomer to produce polyvinyl chloride (PVC). The typical process flow for brine electrolysis includes brine preparation, electrolysis, chlorine treatment, and caustic soda concentration. In this process, almost all equipment comes into contact with highly corrosive media such as high-temperature strong acids, strong alkalis, and chlorine gas, making corrosion a major factor affecting stable production in the chlor-alkali industry.
Currently, the most commonly used anti-corrosion methods in this industry include internal lining or full FRP (fiber-reinforced plastic) structures.
PS material offers excellent resistance to high concentrations of acids, alkalis, salts, and oils. Additionally, it is easy to apply, environmentally friendly, non-toxic, and classified as a “non-hazardous chemical,” making it a highly suitable solution for anti-corrosion applications in chlor-alkali plants.
3. Automotive Industry
PS materials are primarily used in the automotive industry for applications such as instrument panel housings, lamp covers, and lighting components. Polystyrene can also be processed through foaming to produce packaging and thermal insulation materials, which are used in components like car roofs. In addition, PS is often modified or graft-copolymerized with other materials to create various alloy plastics within the PS family. For example, Styrene-Maleic Anhydride (SMA) copolymers are commonly used in the manufacturing of automotive instrument panel frames.
4. Electrical Appliances
PS materials combine excellent transparency with good insulating properties, making them suitable for use in components and housings of televisions, audio recorders, and various electrical appliances, as well as in high-frequency capacitors.
5. Transparent Products
PS has excellent transparency, making it ideal for general optical instruments, transparent models, light covers, instrument housings, and packaging containers.
6. Daily Necessities
With excellent colorability and gloss, PS is widely used in the production of daily necessities, such as children’s toys, decorative panels, cassette cases, furniture handles, combs, toothbrush handles, pen barrels, and stationery.
7. Packaging Materials
PS foam plastics have excellent shock absorption and thermal insulation properties, making them suitable for shockproof packaging and insulation materials. Packaging materials are mainly used for electrical appliances, precision instruments, handicrafts, glass products, and ceramic products; insulation materials include partition boards and sandwich panels for roofs.
Part 4: Production of Polystyrene (PS)
1. Bulk Polymerization
Styrene is polymerized under an inert gas atmosphere at a controlled temperature of 60–90°C using benzoyl peroxide as a catalyst, resulting in a transparent resin in bulk form. This type of resin has high purity, good transparency, and gloss.
2. Emulsion Polymerization
Under the action of a catalyst, a water emulsion of styrene monomer is polymerized at a temperature of 80–95°C. The polymer is then separated from the mother liquor and processed into a powder resin. The final product has slightly better heat resistance than bulk polymerized resin, but slightly lower electrical insulation and transparency.
Part 5: Modification of Polystyrene (PS)
Polystyrene has certain drawbacks, such as brittleness, poor resistance to environmental stress, and poor compatibility. Therefore, performance enhancement through modification is often necessary during production. Common modification methods include compounding modification, copolymer modification, and inorganic nanoparticle modification.
1. Compounding Modification
This involves mechanically blending two or more polymer materials, inorganic materials, and additives to obtain a material with improved mechanical uniformity, thermal properties, and optical properties.
Characteristics of Compounding Modification:
Compounding modification requires low investment and has a short production cycle, making it a key approach for PS modification. It is not only an important method for polymer modification but also a significant way to develop new materials.
PS/PE
Polyethylene (PE) has excellent flexibility and impact resistance, which helps enhance the toughness of PS. However, PS and PE are incompatible polymers, so a compatibilizer must be added during compounding modification.
There are two methods for PS/PE blending: reactive blending and non-reactive blending.
In reactive blending studies, reinforced PS (RPS), hydroxylated PE (CPE), PE, and PS are simultaneously added into a twin-screw extruder for melt blending and extrusion to obtain a modified PS blend.
Note: Increasing the molecular weight of PE does not affect the tensile strength of the blend but can improve its impact strength.
PS/PP
Polypropylene (PP) has higher tensile strength and surface hardness than PS, and better heat resistance. Therefore, blending PP with PS can improve the thermal properties of PS.
However, PP and PS are incompatible, so a compatibilizer is needed. The use of surface-treated silica in the PS/PP system can enhance interfacial adhesion between the polymers and improve the tensile strength of the system. Maleic anhydride-functionalized polypropylene (RPS-MPP) also shows good reactive compatibilization with PS/PP blends.
PS/PC
Polycarbonate (PC) has excellent properties, including good creep resistance and a visible light transmittance of over 90%. Its refractive index is close to that of PS and it can be blended with PS to improve the thermal stability, strength, and toughness of PS.
In partially compatible PS/PC blends, the interface stress is evenly and continuously distributed under external forces, resulting in the formation of crazes and shear bands, which enhance the mechanical properties of the blend.
2. Copolymer Modification
Copolymer modification is one of the important methods for modifying PS. By copolymerizing styrene monomer with a second monomer, flexible groups can be introduced to maintain the excellent original properties of PS while improving its toughness and processing performance. The main methods are block copolymerization and graft copolymerization.
1. Block Copolymerization
PS has low compatibility when blended with other polyolefins, but their copolymerization can yield products with both rigidity and toughness. The second monomer is generally an α-olefin. Using a metallocene catalyst to copolymerize styrene with the second monomer maintains the rigidity of PS while enhancing its flexibility.
2. Graft Copolymerization
Using a metallocene catalyst, styrene is graft-copolymerized with its boron-containing derivatives, and the boron groups in the product are oxidized and hydroxylated.
A series of PS graft copolymers have been synthesized via atom transfer radical polymerization, achieving the functionalization of polystyrene. The grafting density and chain length can be controlled by adjusting the degree of bromination and the amount of added monomer.
Through in-situ chain transfer reactions, terminal polar group-containing PS graft copolymers have been synthesized under appropriate reaction conditions and catalytic systems, enabling the functionalization of PS.
3. Inorganic Nanoparticle Modification
Inorganic nanoparticles exhibit unique surface effects, volume effects, and quantum size effects, making their properties significantly different from conventional powders and bulk materials. By compounding inorganic nanomaterials with PS under specific process conditions, the strength, toughness, heat resistance, and wear resistance of the polymer material can be greatly enhanced. There are several main preparation methods for PS/inorganic nanoparticle composites:
1. Melt Blending Method
Modified nanoparticles are added into the molten resin, and the mixture is blended and molded to obtain the composite product. Since nanoparticles tend to agglomerate and are difficult to disperse uniformly in the system, surface treatment of the nanoparticles before blending is crucial.
PS/nanoparticle composites prepared by mechanical blending can significantly improve tensile strength, notched impact strength, and thermal flow properties.
2. Solution Blending Method
The base resin is dissolved in an appropriate solvent, and nanoparticles are added. After thorough stirring for uniform dispersion, the solvent is removed to obtain the composite.
Multi-walled carbon nanotubes (MWNTs) treated by acid oxidation are dispersed in tetrahydrofuran solution, followed by the addition of PS. After 3 hours of ultrasonic treatment, PS/MWNTs conductive composites are obtained. This method enhances the material’s storage modulus and conductivity.
3. In-situ Polymerization
Surface-treated nanoparticles are added to the monomer and mixed uniformly. Under suitable conditions, polymerization is initiated to prepare PS/nanoparticle composites.
PS/vermiculite nanocomposites prepared by in-situ methods show significantly improved decomposition temperatures compared to pure PS.
Although various modification methods for PS have been developed, the overall performance and modification mechanisms of the modified products still need further improvement. This is because the impact resistance, heat resistance, chemical resistance, and processability of modified products must meet higher standards to enable broader applications of PS-modified materials.
Part 6: What can USEON do in PS Compounding?
Wide Application of USEON Twin-Screw Extruders in PS Compounding
1. Filling Modification:
By adding fillers (such as calcium carbonate, talc, glass fibers, etc.), the rigidity, strength, and heat resistance of PP are improved.
2. Reinforcement Modification:
By incorporating reinforcing materials such as glass fibers or carbon fibers, the mechanical strength and modulus of PP are enhanced.
3. Flame Retardant Modification:
By adding flame retardants, the flame resistance of PP is enhanced, making it suitable for applications requiring flame retardancy.
4. Compounding Modification:
PP is blended with other polymers (such as PE, EVA, EPDM, etc.) to obtain composite materials with superior performance.
5. Functional Modification:
By adding antioxidants, light stabilizers, antistatic agents, etc., PP is endowed with specific functionalities.
Advantages of USEON Extruder
The USEON co-rotating twin-screw extruder offers significant advantages in the modification of polystyrene (PS), especially in processes such as mixing, dispersion, and reactive extrusion. The specific advantages of the co-rotating twin-screw extruder in PS modification are as follows:
1. High-Efficiency Mixing and Dispersion
Uniform Dispersion: The co-rotating twin-screw extruder enables thorough shearing and mixing of materials through the intermeshing action of the twin screws, ensuring uniform dispersion of fillers, toughening agents, antioxidants, and other additives within the polystyrene matrix.
Efficient Compounding: Its high-efficiency compounding capability allows materials to be rapidly and uniformly mixed in the barrel, promoting strong interaction between the modifiers and the base material, thereby enhancing overall material performance.
2. Precise Control of Processing Parameters
Temperature Control: The co-rotating twin-screw extruder is equipped with a precise temperature control system that ensures accurate processing temperatures, maintaining the stability of polystyrene during processing and preventing material degradation.
Shear Rate Control: The shear rate can be adjusted according to the specific material properties and modification requirements to achieve optimal mixing and dispersion results.
3. Strong Adaptability
Flexibility: The co-rotating twin-screw extruder is suitable for various modification processes, including filling, reinforcement, toughening, and flame retardant modification. It is capable of processing a wide range of additives such as glass fibers, mineral fillers, and rubber particles.
Wide Application: It can be used to produce various high-performance modified polystyrene materials, such as High Impact Polystyrene (HIPS), Expanded Polystyrene (EPS), and functionalized polystyrene.
4. High Output and Stability
Continuous Production: The co-rotating twin-screw extruder is ideal for long-duration continuous production, offering high output and efficiency, making it well-suited for large-scale industrial production.
Production Stability: Due to its design features, the co-rotating twin-screw extruder demonstrates excellent process stability during production, ensuring uniform and stable product quality.
5. Energy Efficiency and Environmental Friendliness
High Energy Efficiency: The efficient mixing and processing capabilities of the twin-screw extruder reduce energy consumption while improving material utilization and lowering production costs.
Environmental Friendliness: By optimizing process parameters, waste and emissions during production can be minimized, contributing to a more environmentally friendly production process.
6. Good Scalability
Modular Design: Many co-rotating twin-screw extruders feature a modular design, allowing the screw combinations and extruder configurations to be adjusted according to different processing needs, thereby adapting to various materials and process requirements.
7. Extensive Experience
USEON has successfully delivered over 3,000 twin-screw extruders and has extensive experience in the modification of PP.
FAQs
Yes, polystyrene is recyclable, but the recycling process poses certain challenges. Due to its lightweight and bulky nature, the cost of transportation and processing is relatively high. This is especially true for expanded polystyrene (EPS), which has a large volume and low density, making it even more difficult to recycle. Recycled PS can be used to produce new plastic products or serve as a fuel source.
Polystyrene is difficult to degrade naturally and may take hundreds of years to break down in the environment, placing a long-term burden on ecosystems. If not properly disposed of, PS waste can pollute both marine and terrestrial environments. Expanded polystyrene (EPS), in particular, may break down into microplastics during degradation, posing a threat to wildlife.
Standard polystyrene is generally considered safe for food contact and is commonly used for disposable tableware and food containers. However, PS may release trace amounts of styrene monomer at high temperatures, so it is not recommended for use in microwave heating or for storing hot foods for extended periods.
Compared to other plastics, PS is known for its high transparency and rigidity, but it is more brittle and has poor impact resistance. PP (polypropylene) has better toughness and heat resistance, making it suitable for a wider range of applications. PET (polyethylene terephthalate) also has high transparency and excellent mechanical properties, and is commonly used for beverage bottles and food packaging.
1. Avoid heating containers made of PS in the microwave, especially when they contain fatty foods.
2. When recycling, PS products should be sorted out and compressed as much as possible to reduce volume for easier transport and handling.
3. When discarding expanded polystyrene (EPS), it should be disposed of properly to prevent it from entering the natural environment.